The Future of Manufacturing: Navigating Industry Challenges and Leveraging Top Talent
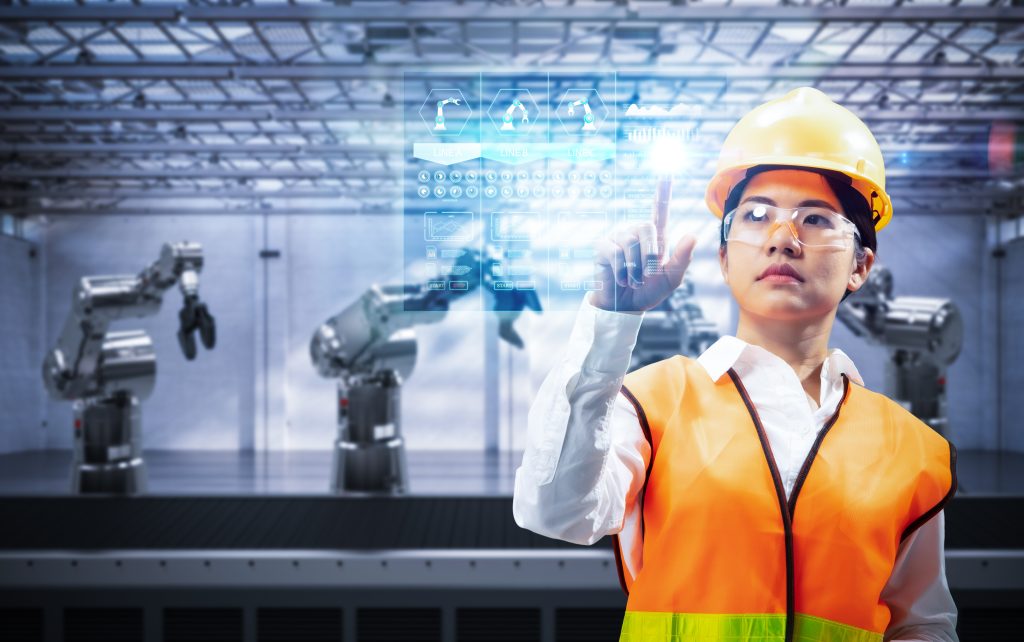
In ultra-modern, fast-paced international, manufacturing is undergoing a metamorphosis. What changed when an enterprise often focused on production efficiency and scaling physical outputs has now advanced into a complicated atmosphere that integrates generation, sustainability, and worldwide supply chain control. Each manufacturing sector faces precise, demanding situations, from automotive to chemical substances and metals to energy. Still, one commonplace denominator stands out—humans.
While machines, automation, and AI might also power modern-day factories, it is the human expertise driving these technologies ahead that ultimately determines achievement. Leaders who power innovation will distinguish themselves from their fans in this ever-converting enterprise.
The Technological Evolution in Manufacturing
Over the last decade, we’ve witnessed an enormous shift in production techniques. Incorporating sensible factories, IoT (Internet of Things) gadgets, and data-driven decision-making has streamlined manufacturing strains, optimized aid control, and made real-time monitoring viable. Artificial intelligence and gadget studying are employed to anticipate machine mistakes, improve quality control, and create more efficient workflows.
However, these improvements include their own set of challenges. New technology requires new competencies, and manufacturers can only rely partially on conventional talent units. They want employees proficient in software engineering, data analytics, robotics, digital generation, manufacturing processes, and hands-on experience. As a result, the demand for surprisingly professional veterans has been more significant, and a competitive landscape for skills acquisition has grown in the manufacturing zone.
The Importance of Impact Players
Having top talent is critical in any enterprise. However, in manufacturing, where precision, safety, and efficiency are paramount, the need for incredibly skilled people who can make impactful contributions is amplified. This is where the idea of Impact Players comes in.
Impact Players are remarkable and contribute disproportionately to a business’s fulfillment. The 20% of the workforce drives 80% of the effects. They convey greater than just their technical talents—they carry innovation, management, and a passion for nonstop improvement. These people excel at their jobs and push the bounds of what is possible, making them necessary for businesses that need to stay competitive in an unexpectedly converting panorama.
In manufacturing, Impact Players are regular folks who can assume severe and creative responsibility to resolve complicated problems, whether it’s enhancing the performance of a production line, designing a sustainable supply chain, or leading the transition to Industry Four Zero technology. These people pressure exchange, and their fees to agencies cannot be overstated.
The Challenge of Labor Shortages
Despite advancements in automation and robotics, human capital remains a crucial issue in production. However, the enterprise is currently facing a labor shortage that has been exacerbated by rapid technological advancements. As manufacturing approaches become more digitized, agencies require people who no longer only comprehend conventional production techniques but can also work with advanced technology.
This demand for a new breed of skilled people has made it increasingly more complex for manufacturers to find the needed talent. Compounding this mission is the getting older staff, and fewer young people are entering the producing area. The notion of manufacturing as a “dirty” or “low-tech” industry persists, notwithstanding trendy factories’ modern-day, excessive-tech nature.
Manufacturers aren’t just seeking out each person to fill vacancies; they’re seeking out innovators, troubleshooters, and leaders who can help them stay ahead in a competitive worldwide market. Finding and attracting those high-caliber individuals has become one of the biggest challenges in today’s enterprise.
Strategies for Talent Acquisition and Retention
Manufacturers need to adopt greater strategic talent acquisition practices to address those challenges. Recruitment in production isn’t always about filling roles—it is about finding the right people to drive the enterprise forward in a more complex environment. Companies should be aware of individuals with the technical abilities, creativity, adaptability, and management characteristics critical in a dynamic production panorama.
Partnering with recruitment firms specializing in manufacturing expertise is a powerful approach to finding these Impact Players. Specialized corporations apprehend the enterprise’s precise needs. They may offer the right of entry to applicants who might not actively seek new possibilities but would suit the employer’s needs.
In addition to recruiting top talent, producers need to focus on retention strategies to keep their great employees engaged and inspired. Offering possibilities for expert growth, offering nonstop education in new technologies, and developing a nice place of work life are all vital additives to employee retention.
Training and upskilling packages are crucial in the present-day environment. As technology evolves, even the most skilled people ought to keep learning to stay relevant. Offering employees the risk to expand their abilities and take on more challenging roles benefits the business enterprise. It keeps employees engaged and invested in their long-term careers within the organization.
Building the Future of Manufacturing
Organizations that incorporate new technology and understand the importance of building robust teams may shape the destiny of production. Investing in technology and talent is important to staying ahead in a changing industry.
Attention must be paid to lengthy-term expertise acquisition strategies that prioritize identifying and nurturing Impact Players. These individuals will help put pressure on innovation, performance, and resilience to succeed in an unexpectedly changing international landscape. Moreover, manufacturers should continue adapting by fostering a workplace culture emphasizing collaboration, continuous learning, and sustainable growth.
In conclusion, production businesses that prioritize strategic recruitment and employee development will function for fulfillment. While era performs a critical role, the human element—the skills, creativity, and management of Impact Players—will, in the long run, define the enterprise’s future.
FAQs –
Q. How is technology impacting the manufacturing industry?
A. Technology is revolutionizing manufacturing through innovations such as smart factories, IoT, AI, and machine learning. These advancements streamline production, optimize resource management, and enhance decision-making processes, but they also require a workforce with new technical skills.
Q. What are Impact Players, and why are they important in manufacturing?
A. Impact Players are the top 20% of the workforce who contribute disproportionately to a company’s success. In manufacturing, they bring technical expertise, leadership, and innovation that push the industry forward. These individuals are essential for solving complex challenges and staying competitive.
Q. Why is there a labor shortage in the manufacturing industry?
A.The labor shortage is primarily due to the rapid digitization of manufacturing, which demands new skills that traditional workers may lack. Additionally, fewer younger people are entering the industry, and the perception of manufacturing as “low-tech” persists despite advancements.
Q. How can manufacturers attract and retain top talent?
A.Manufacturers need to adopt strategic recruitment practices by partnering with specialized talent firms, offering continuous training, and providing career growth opportunities. Retaining talent involves creating a positive workplace culture and offering ongoing professional development to keep employees engaged and motivated.
Conclusion
The future of manufacturing hinges on a delicate balance between technological advancements and human capital. While smart factories, automation, and AI are reshaping the industry, it’s the skilled workforce—particularly Impact Players—that will drive innovation, solve complex problems, and push boundaries.
Manufacturers that understand the importance of combining technology with top talent will lead the way in navigating industry challenges. They must adopt strategic recruitment and retention practices, invest in upskilling and continuous learning, and create a work environment that fosters collaboration and growth. By focusing on both technology and talent, manufacturers can build resilient, innovative companies poised to thrive in an increasingly complex global landscape.