How To Overcome Challenges In Manufacturing and Maintenance
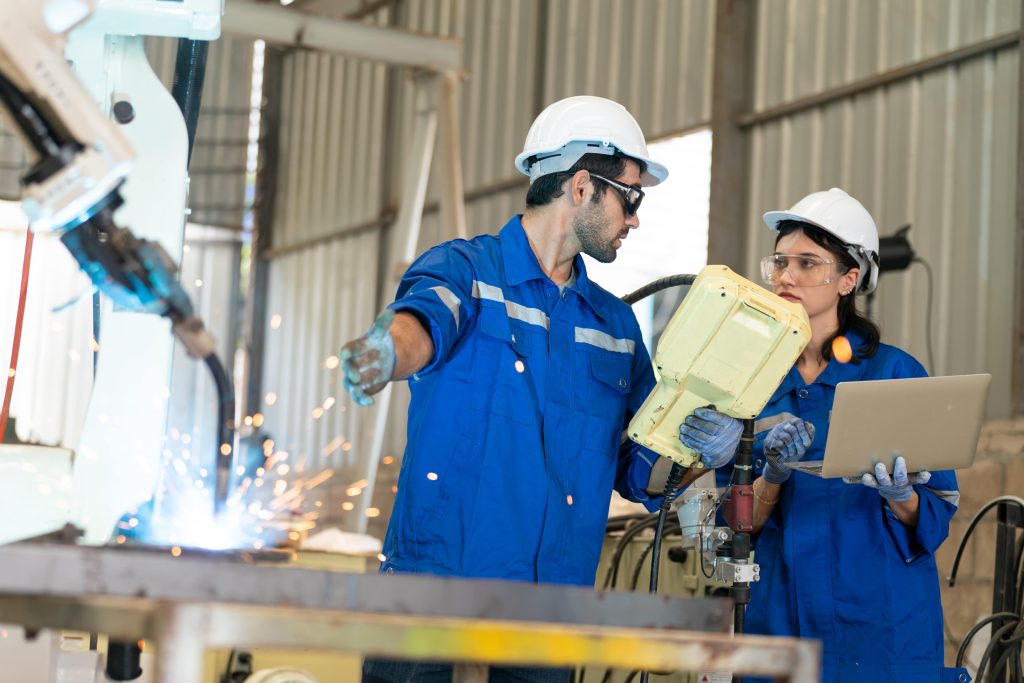
The manufacturing and facility maintenance sectors need help with operational efficiency and productivity. These obstacles can significantly impact a company’s bottom line, from unplanned downtime and equipment failures to regulatory compliance and workforce productivity issues.
Addressing these challenges is very important for businesses to remain competitive and maintain a streamlined operation.
Identifying Major Challenges
Key Manufacturing Challenges
- Unplanned downtime: Unscheduled production line stoppages, typically due to equipment breakdowns or unforeseen issues, can result in costly delays and decreased productivity.
- Equipment failures: Aging or poorly maintained machinery and equipment are prone to breakdowns, which disrupt operations and require expensive repairs or replacements.
- Regulatory compliance: Manufacturing companies constantly face the challenge of ensuring compliance with industry regulations, safety standards, and environmental laws.
- Inventory management: Careful planning and monitoring are required to maintain optimal inventory levels, minimize excess stock, and prevent shortages.
- Workforce productivity: Ensuring employees are properly trained, motivated, and equipped to maximize their productivity can be a significant hurdle.
- Energy management: Increasing energy costs and environmental concerns necessitate efficient energy management practices in manufacturing facilities.
Primary Facility Maintenance Challenges
- Complicated inspections: Conducting thorough and accurate assessments of complex systems and equipment can be time-consuming and difficult.
- Service request management: Efficiently tracking, prioritizing, and addressing maintenance requests can be a logistical challenge, especially in large facilities.
- Mobile flexibility for maintenance tasks: Enabling technicians to access and update maintenance information on the go can improve efficiency and responsiveness.
- Cost and budget adjustments: Balancing maintenance costs with budget constraints and finding cost-effective solutions is an ongoing challenge.
- Lean manufacturing impacts on maintenance: Implementing lean manufacturing principles can require significant maintenance strategies and process changes.
Strategies for Overcoming Challenges
Downtime Reduction and Equipment Reliability
- Predictive maintenance techniques: Data analysis and machine learning algorithms will predict when equipment will require maintenance, enabling proactive repairs and reducing unplanned downtime.
- Real-time monitoring systems: Deploy cutting-edge sensors and advanced monitoring systems to proactively track equipment performance and identify potential issues before they escalate. Implementing sensors and monitoring systems to track equipment performance and identify potential issues before they escalate.
- Scheduled maintenance routines: Adhering to regular maintenance schedules to ensure equipment is properly serviced and maintained, minimizing the risk of breakdowns.
- Case study: A manufacturing plant implemented a predictive maintenance program and saw a 20% reduction in unplanned downtime, resulting in significant cost savings.
Ensuring Regulatory Compliance and Safety
- Keeping up-to-date with regulations: Regularly reviewing and updating compliance protocols to align with the latest industry regulations and standards.
- Employee training & awareness programs: Provide proper training and educational resources to ensure employees understand and follow compliance requirements.
- Compliance management software: Utilizing specialized software to streamline compliance processes, document management, and reporting.
- Example: A facility implemented a comprehensive compliance management system, including employee training and automated reporting, ensuring consistent safety and adherence to environmental regulations.
Adequate Inventory and Workforce Management
- Just-in-time inventory systems: Implementing lean manufacturing principles to minimize excess inventory and reduce storage costs while ensuring timely materials delivery.
- Automated inventory tracking: Using barcode scanning, RFID, or other technologies to accurately track inventory levels and movements.
- Training and development programs: Invest in training and development to enhance employee skills, productivity, and job satisfaction.
- Utilizing technology and automation: Implementing automated systems and processes to streamline workflows and reduce manual labor, where appropriate.
- Example: A manufacturing company introduced automated inventory tracking and lean manufacturing principles, resulting in a 30% reduction in inventory costs and a 15% increase in workforce productivity.
Optimizing Energy Management
- Energy-efficient equipment: Upgrading to more energy-efficient machinery and equipment to reduce overall energy consumption and costs.
- Monitoring energy usage: Installing energy monitoring systems to identify areas of high consumption and potential opportunities for improvement.
- Implementing energy-saving practices: Promoting and mandating energy-saving practices, including powering down equipment when idle and maximizing the efficiency of heating and cooling systems.
- Example: A large manufacturing facility implemented a comprehensive energy management program, which included energy-efficient equipment upgrades, monitoring systems, and employee awareness campaigns, resulting in a 25% reduction in energy costs.
Addressing Facility Maintenance-Specific Issues
Streamlining Inspections and Service Requests
- Maintenance management software: Utilizing specialized software to centralize and automate maintenance tasks, inspections, and service requests.
- Mobile solutions for on-the-go maintenance: These solutions enable technicians to access and update maintenance information from mobile devices, improving efficiency and responsiveness.
- Efficient scheduling and tracking systems: Implementing systems to prioritize and track maintenance tasks, ensuring timely completion and proper allocation of resources.
- Case study:A facility implemented a mobile-enabled maintenance management system, which allowed technicians to access and update information in real-time. This resulted in a 30% increase in maintenance productivity.
Adapting to Budget and Cost Constraints
- Cost-benefit analysis for maintenance activities: Evaluating the costs and benefits of maintenance activities to prioritize critical tasks and allocate resources effectively.
- Prioritizing critical maintenance tasks: Identifying and addressing the most essential maintenance tasks first to minimize the risk of costly breakdowns or operational disruptions.
- Leveraging cost-effective solutions: To reduce costs, explore alternative solutions, such as refurbished equipment or outsourcing specific maintenance tasks.
- Example: A facility conducted a comprehensive cost-benefit analysis and implemented a prioritized maintenance plan, focusing on critical tasks and leveraging cost-effective solutions. This resulted in a 15% reduction in maintenance costs.
Implementing Lean Manufacturing in Maintenance
- Integrating lean principles into maintenance processes: Adapting lean manufacturing principles, such as minimizing waste, continuous improvement, and standardization, to maintenance operations.
- Continuous improvement practices: Encouraging and facilitating constant improvement initiatives to streamline maintenance processes and eliminate inefficiencies.
- Eliminating waste and improving efficiency: Identifying and removing non-value-added activities, optimizing workflows, and improving maintenance efficiency.
- Case study:A manufacturing plant implemented lean maintenance practices, including standardized procedures, continuous improvement initiatives, and waste elimination, resulting in a 25% increase in maintenance efficiency and cost savings.
FAQs
Q. What are the most common challenges in manufacturing maintenance?
A. The most common challenges include unplanned downtime, equipment failures, regulatory compliance, inventory management, workforce productivity, and energy management.
Q. How can downtime be reduced in manufacturing operations?
A. Implementing predictive maintenance techniques, real-time monitoring systems, and scheduled maintenance routines can significantly reduce unplanned downtime.
Q. What strategies can be implemented to prevent equipment failures?
A.Regular maintenance, predictive maintenance, and real-time monitoring can help identify potential issues and avoid equipment failures.
Q. How can companies ensure regulatory compliance?
A. Staying up-to-date with regulations, providing employee training, and utilizing compliance management software can help maintain regulatory compliance.
Q. What are effective ways to manage inventory in manufacturing?
A. Just-in-time inventory systems, automated inventory tracking, and lean manufacturing principles can optimize inventory management.
Q. How can workforce productivity be improved in maintenance tasks?
A. Investing in employee training, utilizing technology and automation, and implementing efficient scheduling and tracking systems can boost workforce productivity.
Q. What are the best practices for energy management in manufacturing facilities?
A. Upgrading energy-efficient equipment, monitoring energy usage, and implementing energy-saving practices can optimize energy management.
Q. How can inspections and service requests be streamlined?
A. Maintenance management software, mobile solutions, and efficient scheduling and tracking systems can streamline them.
Q. What are the cost-effective strategies for facility maintenance?
A. Conducting cost-benefit analyses, prioritizing critical tasks, and leveraging cost-effective solutions can help reduce maintenance costs.
Q. How does lean manufacturing impact facility maintenance?
A. Implementing lean principles, such as continuous improvement and waste elimination, can improve the efficiency and cost-effectiveness of maintenance operations.
Conclusion
Overcoming the challenges the manufacturing and facility maintenance sectors face requires a multifaceted approach.
To maintain a competitive edge, companies should implement predictive maintenance, regulatory compliance programs, lean manufacturing principles, and energy management initiatives to improve operational efficiency and reduce costs.
As technology advances, new solutions and best practices will emerge, presenting opportunities for further improvement and adaptation.
Staying proactive, embracing continuous improvement, and leveraging the latest tools and techniques will be crucial for manufacturers and facility managers to stay ahead of the curve and overcome evolving challenges.