5 Ways Manufacturers Can Build Towards a Digital Future
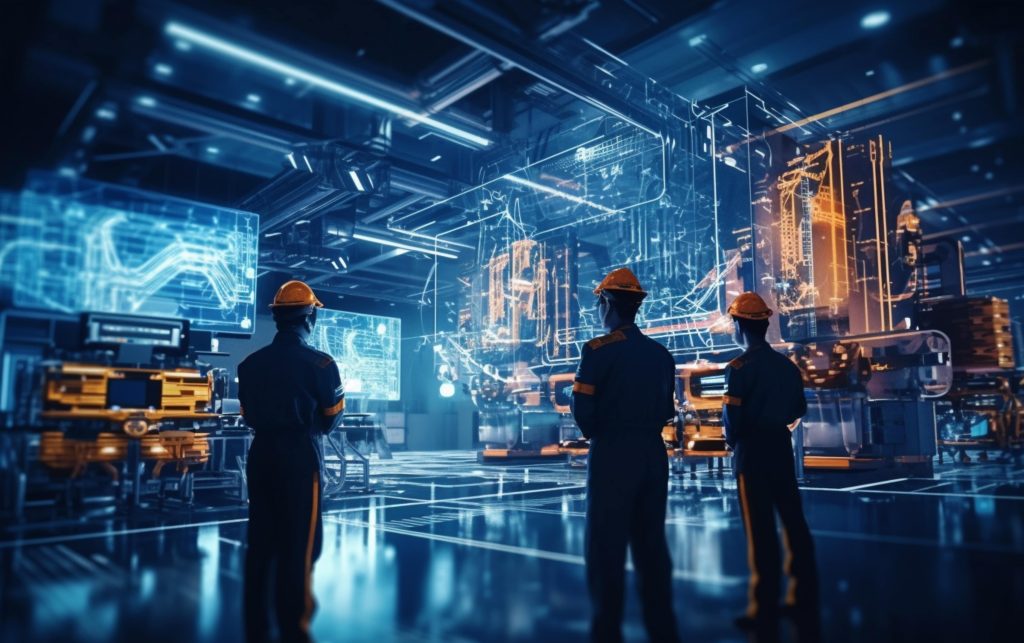
The manufacturing sector is facing intense competitive pressures and evolving market demands. Consequently, Digital transformation is necessary for manufacturers to stay ahead of the curve.
According to a recent report by McKinsey, companies that have embraced digital technologies experienced a staggering 16% increase in productivity compared to their non-digital counterparts.
Adopting these 5 strategies can help you move toward a digital future if you’re a manufacturer looking to future-proof your business.
Embracing Industry 4.0 Technologies
What is Industry 4.0?
Specifically, Industry 4.0 is the 4th industrial revolution, combining advanced technologies into manufacturing processes. It encompasses the following key components:
- Internet of Things: IoT allows us to monitor and perform real-time predictive maintenance by connecting devices and machines to the Internet, facilitating seamless data exchange.
- Artificial Intelligence (AI) and Machine Learning: AI and machine learning algorithms can optimize quality control processes and identify patterns in production data, leading to improved efficiency and reduced waste.
- Big Data: With advanced data collection, storage, and analysis capabilities, manufacturers can make informed decisions based on real-time insights.
- Robotics: Automated systems and robots can handle redundant tasks, letting workers focus on more challenging and valuable activities.
Success Stories
For example, companies like Ford and Siemens have successfully implemented Industry 4.0 technologies, resulting in enhanced efficiency, reduced downtime, and improved product quality.
For instance, Ford’s use of IoT sensors and predictive analytics has reduced unplanned downtime by 25%, translating into substantial cost savings.
Developing a Digital Culture
Cultivating a Digital Mindset
Moreover, fostering a digital culture is crucial for manufacturers to thrive in the digital age. A digital-first mindset is needed at every level, from leadership to frontline workers.
Therefore, to cultivate a digital culture, manufacturers should consider the following strategies:
- Training Programs: Implement continuous education and training programs to provide employees with digital skills and knowledge.
- Leadership Commitment: Leaders must champion digital transformation initiatives and lead by example, embracing new technologies and encouraging innovation.
- Employee Engagement: Encourage employees to provide feedback and ideas for improving digital processes, fostering a culture of innovation and continuous improvement.
Case Studies
For example, companies like Unilever and Bosch have successfully cultivated a digital culture by investing in employee training, implementing digital collaboration tools, and incentivizing innovation.
Moreover, as we integrate these technologies, investing in cybersecurity becomes essential to protect our progress.
Investing in Cybersecurity
Protecting Digital Assets
Therefore, as manufacturers adopt digital technologies, ensuring the security of digital assets and data integrity becomes paramount. Consequently, cybersecurity threats like phishing attacks, malware, and IoT vulnerabilities pose significant risks to manufacturing operations and intellectual property.
To mitigate these risks, manufacturers should implement the following best practices:
- Robust Security Protocols: Implement multiple layers of security, such as firewalls, access controls, and encryption, to defend against cyber threats.
- Regular Audits: Conduct security assessments and updates for new threats and vulnerabilities.
- Employee Training: Educate employees on recognizing and mitigating security threats, as human error is often a leading cause of cyber breaches.
Learning from Past Incidents
In 2017, a major cyber attack disrupted operations at Renault and Nissan, resulting in significant production losses and financial damages. This incident is a cautionary tale, highlighting the critical need for strong cybersecurity measures in the manufacturing sector.
Leveraging Data Analytics
The Power of Data-Driven Decision-making
Indeed, data analytics revolutionizes modern manufacturing, empowering informed decision-making through real-time insights and historical data analysis. There are 3 main types of data analytics:
- Descriptive Analytics: Understanding past performance by analyzing historical data.
- Predictive Analytics: Forecasting future trends and performance based on historical patterns and machine learning models.
- Prescriptive Analytics: Recommending specific actions based on data-driven insights for optimal outcomes.
Tools and Technologies
Manufacturers can use tools and technologies to harness the power of data analytics, such as:
- Data Management Platforms: Software and platforms designed for data integration, storage, and analysis, enabling seamless access to actionable insights.
- AI and Machine Learning: Advanced algorithms uncover hidden patterns and correlations in large datasets, improving predictive and prescriptive analytics accuracy.
For instance, companies like Amazon and Walmart have successfully executed data analytics for their supply chain operations, resulting in improved forecasting, enhanced customer insights, and increased operational efficiency.
Building a Flexible and Scalable IT Infrastructure
The Foundation for Digital Transformation
Importantly, a robust and flexible IT infrastructure is the backbone of digital transformation, enabling manufacturers to seamlessly integrate new technologies and adapt to changing business needs.
Key components of a modern IT infrastructure include:
- Cloud Computing: Offering scalability, flexibility, and cost-effectiveness, cloud computing allows manufacturers to scale resources up or down based on demand.
- Edge Computing: Edge computing reduces latency, enables real-time processing, and is crucial for IoT and automation applications by processing data to the source.
- Enterprise Resource Planning (ERP): The ERP systems integrate business processes, inventory management, supply chain management, and finance, enabling better management and decision-making.
Strategies for Success
To build a scalable IT infrastructure, manufacturers should consider the following strategies:
- Scalability: Ensure the infrastructure can grow and adapt to changing business needs, minimizing disruptions and enabling seamless expansion.
- Integration: New technologies should seamlessly integrate existing systems, enabling data exchange and collaboration across departments.
- Maintenance: Regular updates and maintenance are important to ensure the IT infrastructure’s reliability, security, and optimal performance.
For instance, Companies like Toyota and GE have successfully built robust IT infrastructures, enabling improved collaboration, reduced costs, and enhanced productivity across their global operations.
FAQs
Q. What are the key benefits of digital transformation for manufacturers?
A. Digital transformation offers manufacturers numerous benefits, including improved efficiency, reduced costs, enhanced product quality, and increased agility to respond to market changes.
Q. How can manufacturers start their digital transformation journey?
A. Manufacturers should develop a comprehensive digital strategy aligning with their business goals. Start with small projects to test new technologies before scaling across the organization. Invest in employee training and change management for a successful digital transformation.
Q. What challenges do manufacturers face during digital transformation?
A. Common challenges include employee resistance to change, high initial costs associated with new technologies, and cybersecurity risks arising from increased connectivity and digitalization.
Q. How does digital transformation impact the manufacturing workforce?
A. Digital transformation will require the workforce to upskill and reskill to adapt to new technologies and processes. While some jobs may be displaced by automation, new roles, such as data analysts, robotics engineers, and cybersecurity specialists, will emerge.
Conclusion
In summary, digital transformation has become a necessity rather than an option for manufacturers to remain competitive and innovative in the digital age.
By embracing Industry 4.0 technologies, cultivating a digital culture, investing in cybersecurity, leveraging data analytics, and building a flexible IT infrastructure, manufacturers can future-proof their operations and succeed in the digital landscape.
Remember, the journey toward digital transformation is not a one-time effort but a continuous process of adaptation and improvement.
So, what are you waiting for?
Start your digital transformation journey today and unlock your manufacturing business!